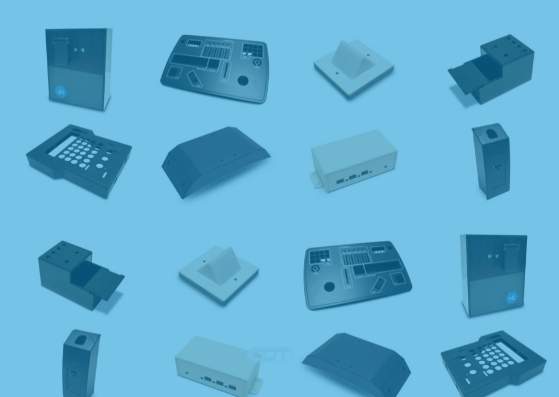
Trying to decide which plastic manufacturing process is best suited for your enclosure project? Here is a quick overview of some of the critical factors that may affect your decision about whether to use plastic injection moulding vs custom plastic machining.
What is the difference between plastic injection moulding and custom plastic enclosure manufacturing?
The plastic injection moulding process heats solid plastic pellets until they melt, then injects them into a mould. When the plastic cools, the mould is removed, leaving a shaped enclosure.
The custom plastic machining process uses a sheet of plastic that is machined into the enclosure shape using specialist machinery. So how do you choose between these plastic manufacturing processes? Here are some pointers:
Speed to market
Typically our custom enclosure manufacturing process takes 1 to 2 weeks to prototype and 4 to 5 weeks for manufacturing making it a lot quicker than injection moulding which can take between 6 to 9 months to get to the same stage so if speed to market is important then custom enclosure manufacturing wins hands down!
Quantity is a crucial factor when deciding between injection moulding and custom machining
The amount required is the key driver in this decision mainly because it dictates the price per unit. Custom enclosure manufacturing is generally cheaper than injection moulding for smaller production runs. This is because the process does not need to use moulds or tools, which means that there are no expensive moulds to produce or steel tooling to cut. Usually, custom enclosure manufacturing becomes less cost-effective when the order quantity exceeds batch sizes of 10,000.
Custom enclosures are thus more cost-effective for prototype development and affordable for start-ups to test their market.
Enclosure design longevity
If you are likely to need to change the design of your custom plastic case in the near future, then it is not usually financially viable to invest in another expensive mould tool.
Instead, it is best to machine your parts as you will not only avoid spending thousands on a tool you can no longer use. You also benefit from the ability to change the design easily at any point. Plastic machining is known for being a more flexible manufacturing process. For example, after the initial order, you could decide to amend or add a component to your box when you re-order. This is easily done quickly with no fuss or additional costs.
Use of advanced speciality plastics
Your selection of plastic materials is generally more limited with injection moulding. Rubbers and other flexible materials are ideal for moulding; however, many harder, high-performance speciality plastics can only be machined.
Also, worth noting that with machining, you can have different material options within the same production run.
In conclusion
So, to conclude, consider custom plastic machining if you require fast turnaround times, cost efficiency for low quantities and flexibility of design.
Call us on 01280 845530 for your next enclosure prototype project, or medium production run, and you will enjoy smoother, faster, cost-effective custom plastic manufacturing that has no minimum order quantities.